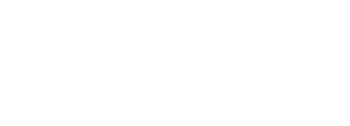
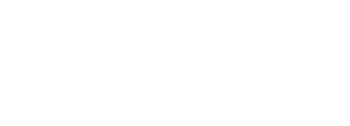
2035 avenue Victoria bur. 306,
Saint-Lambert (QC), J4S 1H1
Téléphone : 450 655-5115
info@plasticompetences.ca
2035 avenue Victoria bur. 306,
Saint-Lambert (QC), J4S 1H1
Téléphone : 450 655-5115
info@plasticompetences.ca
Avec la participation financière de la
Avec la participation financière de la
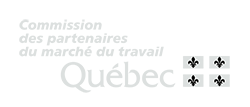
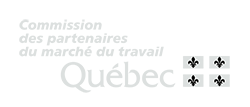
Pour plus de renseignements sur le
marché du travail et sur les
programmes et services publics d’emploi,
consultez le site de Services Québec :
www.quebec.ca/services-quebec
Pour plus de renseignements sur le
marché du travail et sur les
programmes et services publics d’emploi,
consultez le site de Services Québec :
www.quebec.ca/services-quebec
© 2023 PlastiCompétences inc. Tous droits réservés.